The Modern Cabin Solution for Train Manufacturers and Operators
Lightweight, durable and approved for safety. INNOCAB® is considered a trendsetter for modern cabin design. The efficient use of composites in the mobility sector is rapidly growing. Composite modules are increasingly being used to strengthen the structure of trains, tramways, subways, buses, planes and boats. INNOCAB® offers all the benefits of traditional materials to create a successful train concept. Since 1989, INNOCAB® products have served in the daily routine on many international railway networks.
Overview
The unit’s solid foam core, fibre-reinforced plastic and cover layers are engineered for high quality, durable, modern-looking trains and rail front end cabins. By design, INNOCAB® is an ideal answer to demanding customer applications and is consistently developed for the future.
INNOCAB® Advantages
- Stiff and rigid structure offers a safe work environment for train personnel
- Non-corrosive materials ensure long-lasting performance
- Essential weight reduction supports energy savings
- Thinner walls allow a more spacious cabin interior, providing increased passenger comfort and ergonomics
- Minimized repair time
- Damages can be fixed in-house by use of a cold repair method
- Simplified repair process: modular design makes for easy part replacement
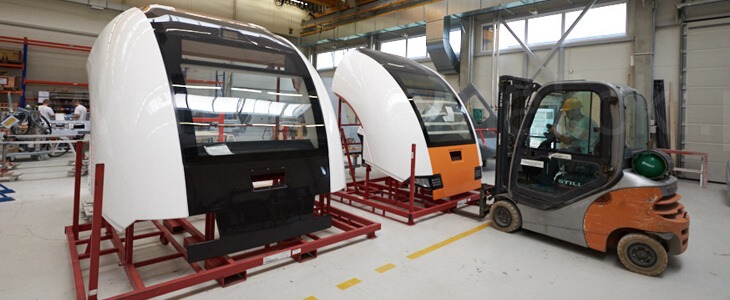
INNOCAB® in Service
- Certified production processes ensure consistent product quality to demanding industry standards
- Resistance to impact and heat
- Fire protection, noise insulation
- Ready-to-install modules: pre-assembled systems are delivered fully equipped
- Customized according to customer design and specifications
- Reduced number of parts shorten assembly time
- Systems are provided ready-to-go
- Optional water or solvent based painting
Production Technologies
Based on the customer order, INNOCAB® can be offered with the use of three distinctive production technologies: Hand lamination – for smaller volumes; Vacuum Assisted Resin Infusion (VAC) – for high volumes; or Vacuum Infusion Process – developed for highest stability. All technologies offer superior product properties and high surface quality.
Vacuum Assisted Resin Infusion (VAC)
- Technological competence from CAD design and engineering to ready-to-install modules
- Designated for producing high-quality, large-scale structural elements
- Design based on solid foam or cores covered with fibre-reinforced resins and gel-coated skins
- Process includes core bonding for reduced manufacturing time
- Inserts for quick interior element installation can be added during the manufacturing process
- INNOCAB® systems are available from unfinished, primed, coated finish, partly assembled up to ready for assembly
Vacuum Infusion Process
- Cost-efficient process for ultra-lightweight and extremely stable composite parts
- Product offers increased stiffness and durability levels compared to standard common composite production technologies
- Capable for composites with higher fibre content for improved overall product properties
- Cabin fronts (including interior) can be completed with a choice of coated finish
Water or Solvent Based Painting
- Large-sized front ends coated in top modern painting infrastructure with humidity and temperature control system
- Applicable for a wide range of coating systems
- Multicolor surface option available
- Full range of test equipment according to specifications
- High-class surface quality
Safe, Durable, Impact-Resistant (Speeds up to 600 km/h)
INNOCAB® offers weight reduction and increased strength made possible by a combination of carefully selected materials. The module’s fibre-reinforced plastic, combined with high quality solid foam, ensures noise reduction and heat insulation while achieving all required fire protection standards.
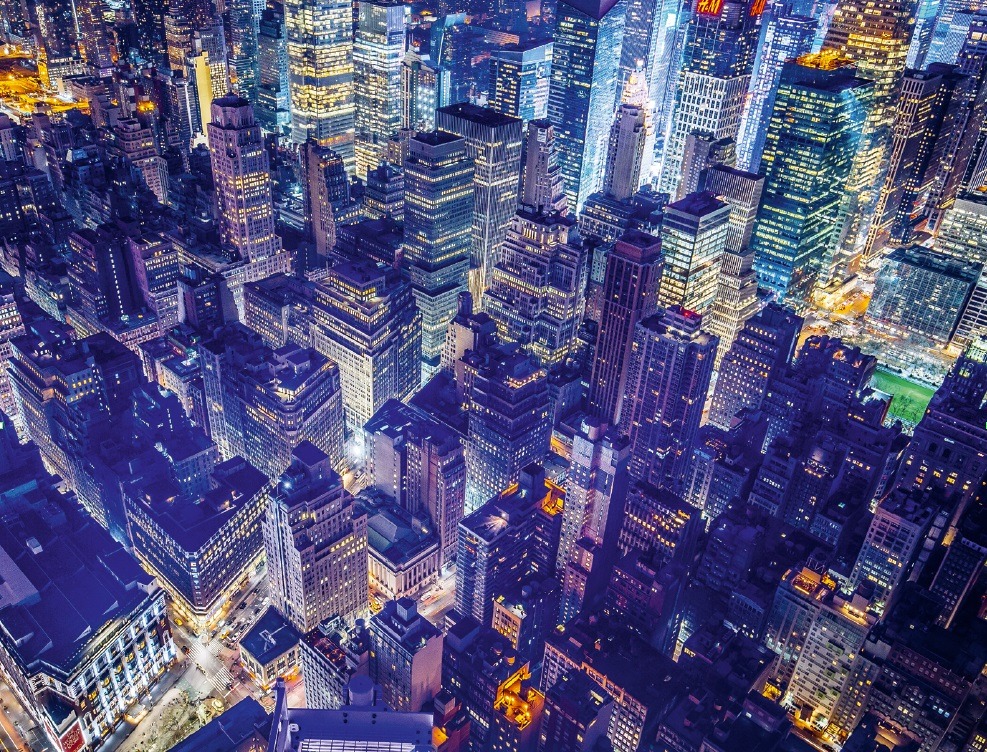
Less Is More
INNOCAB® provides a lightweight structure that improves overall performance. Efficient system integration ensures that fewer components are required per unit.
A Low-Maintenance, Cost-Effective and Time-Saving Solution
INNOCAB® modular system significantly reduces unit assembly time. Existing cabin design upgrades or entirely new cabin concept installations are developed efficiently and require a minimum of tooling investment. INNOCAB® systems are low-maintenance and require minimal lifecycle investment. In the case of element damage, the unit’s sandwich technology allows train manufacturers and operators to directly apply certified panel repair systems. Smaller damages can be fixed at local workshops, while structural damages can typically be brought in for repair by qualified personnel at designated service centres.

INNOCAB® Brochure
684.49 KB, PDF
Download