Autor: Mariola Moskal
Aktualności
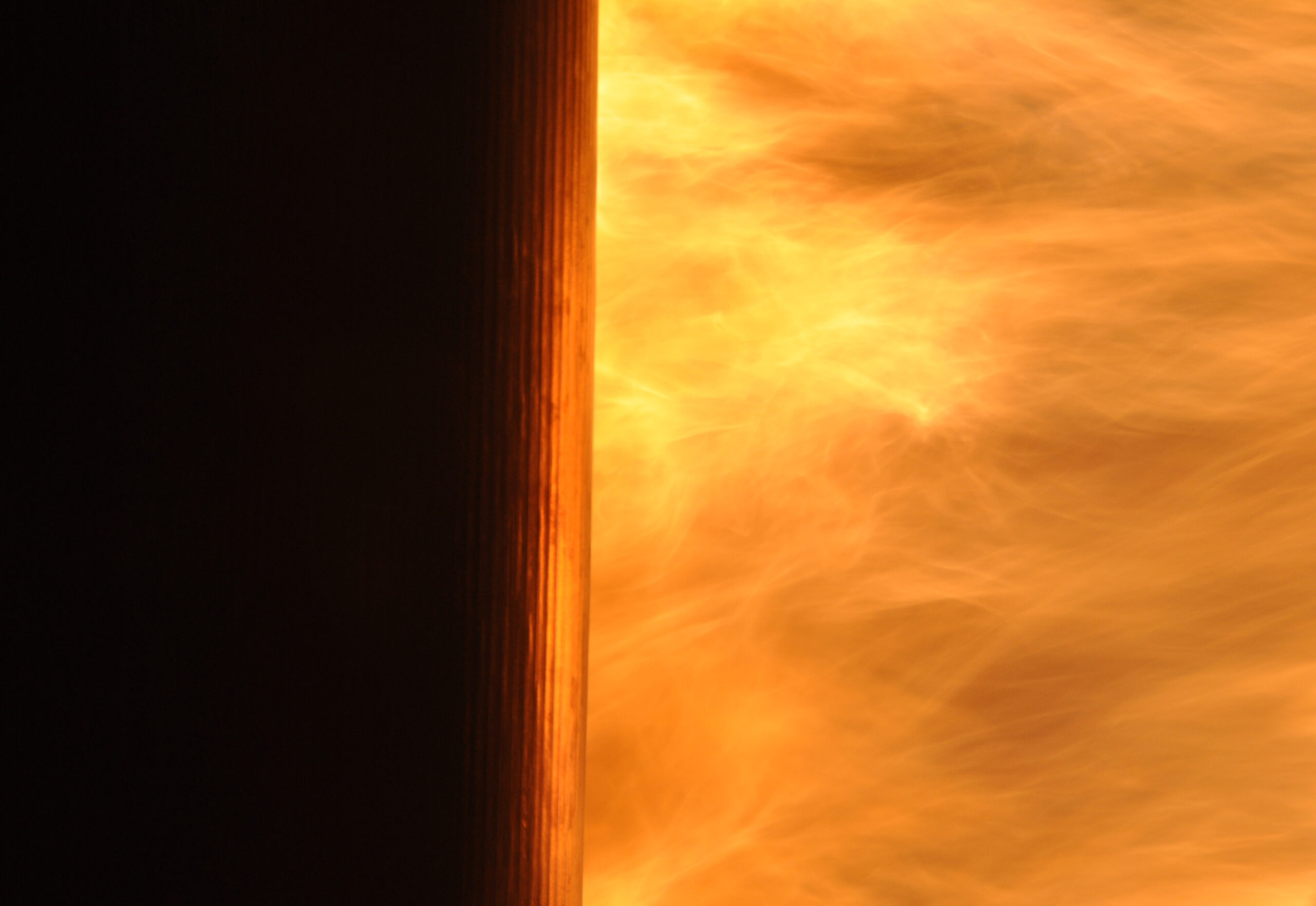
Kolejny miesiąc, kolejny cel osiągnięty przez zespół 3A Composites Mobility. Dumnie informujemy, że uzyskaliśmy poziom HL3 normy palnościowej EN-45545 – czyli najwyższy poziom dla R17 – pełny system z lakierem. Dbamy o wysoką jakość naszych produktów dlatego nasze systemy nie zawierają materiałów na bazie szkodliwego fenolu. Dzięki temu osiągnięciu, możemy produkować elementy warstwowe typu sandwich, które będą miały zastosowanie w ścianach czołowych pojazdów szynowych.
Ochrona przeciwpożarowa w pojazdach szynowych – Norma EN 45545 – określa wymagania materiałowe dla poszczególnych poziomów zagrożenia w różnych częściach pojazdów. Nasi inżynierowie pracowali w ostatnich tygodniach, aby osiągnąć kolejny cel w naszych założeniach i nieustannie dostarczać najbardziej innowacyjne oraz inteligentne rozwiązania dla przyszłości transportu.
Intensywnie wykonywaliśmy szereg testów zgodnie z normą EN-45545 w akredytowanych laboratoriach palnościowych, aby uzyskać najwyższą jakość dostarczanych elementów dla naszych klientów.
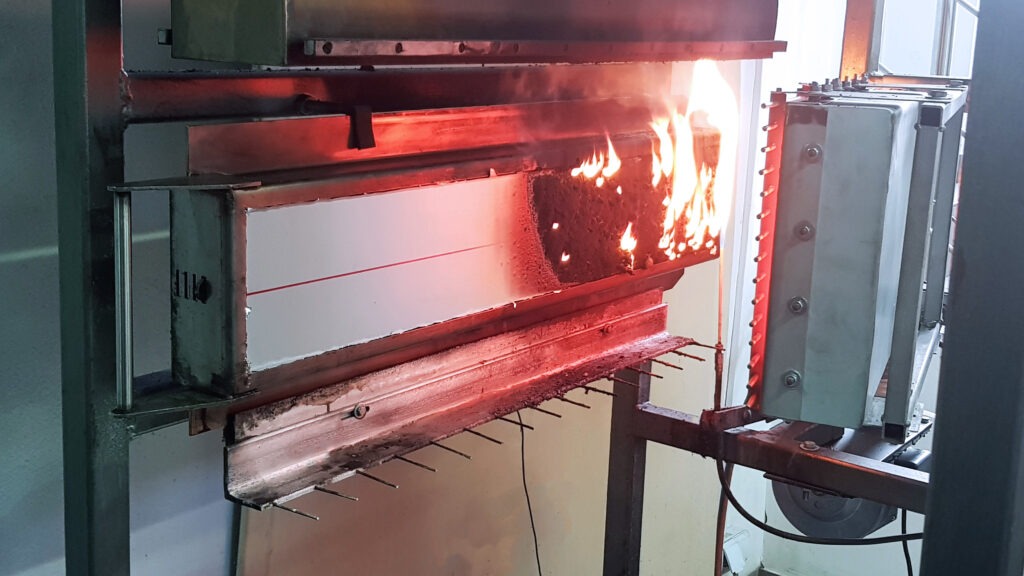
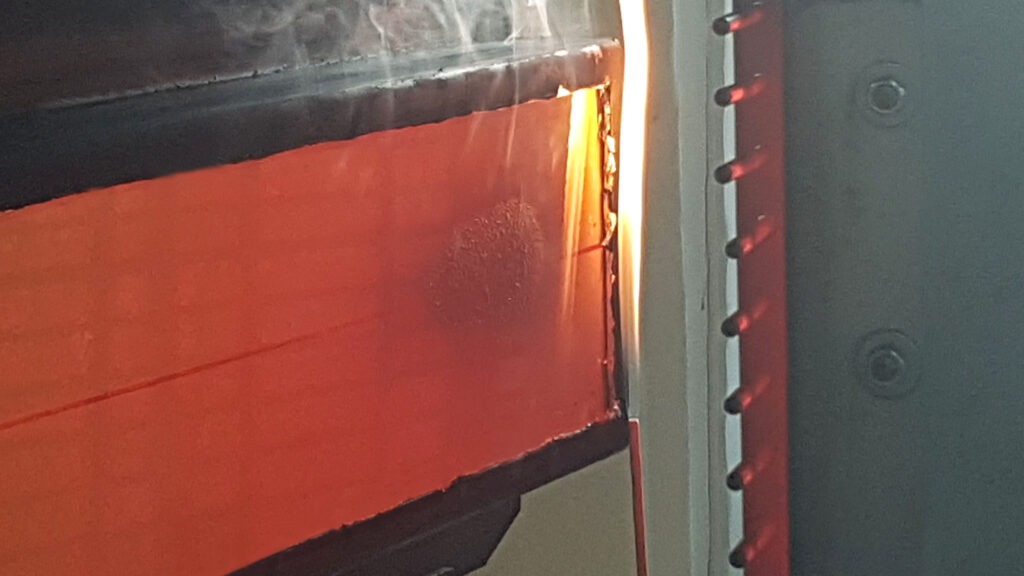
Przeprowadzaliśmy badania takie jak:
1. CFE-ISO 5658-2
Ta metoda polega na przeniesieniu się płomienia wzdłuż próbki do momentu samoistnego zgaśnięcia lub zakończenia czasu trwania badania. Pozwala to określić długość spalonej części próbki w celu wyliczenia krytycznego strumienia ciepła CFE [kW/m²]. Metoda wykorzystywana jest do określania rozprzestrzeniania płomienia.
2. MAHRE ISO 5660-1
W tym teście próbka poddawana jest działaniu promieniowania za pomocą elektrycznego promiennika stożkowego. Metoda ta bada maksymalną średnią szybkość wydzielania ciepła [kW/m²] w czasie 20 minut testu. Celem badania jest ustalenie intensywności wydzielania ciepła przez próbkę.
3. Ds./VOF/CIT ISO 5659-2
Próbka poddawana jest promieniowaniu cieplnemu w zamkniętej komorze, aby wskazać właściwą gęstość optyczną Ds oraz VOF₄ – wartość zaciemnienia w 4 minucie. To badanie określa stężenia poszczególnych gazów w wydzielanym dymie, oraz wyliczyć ich indeks toksyczności – CITG [-]. Ten test pozwala zbadać intensywność wydzielania dymu.
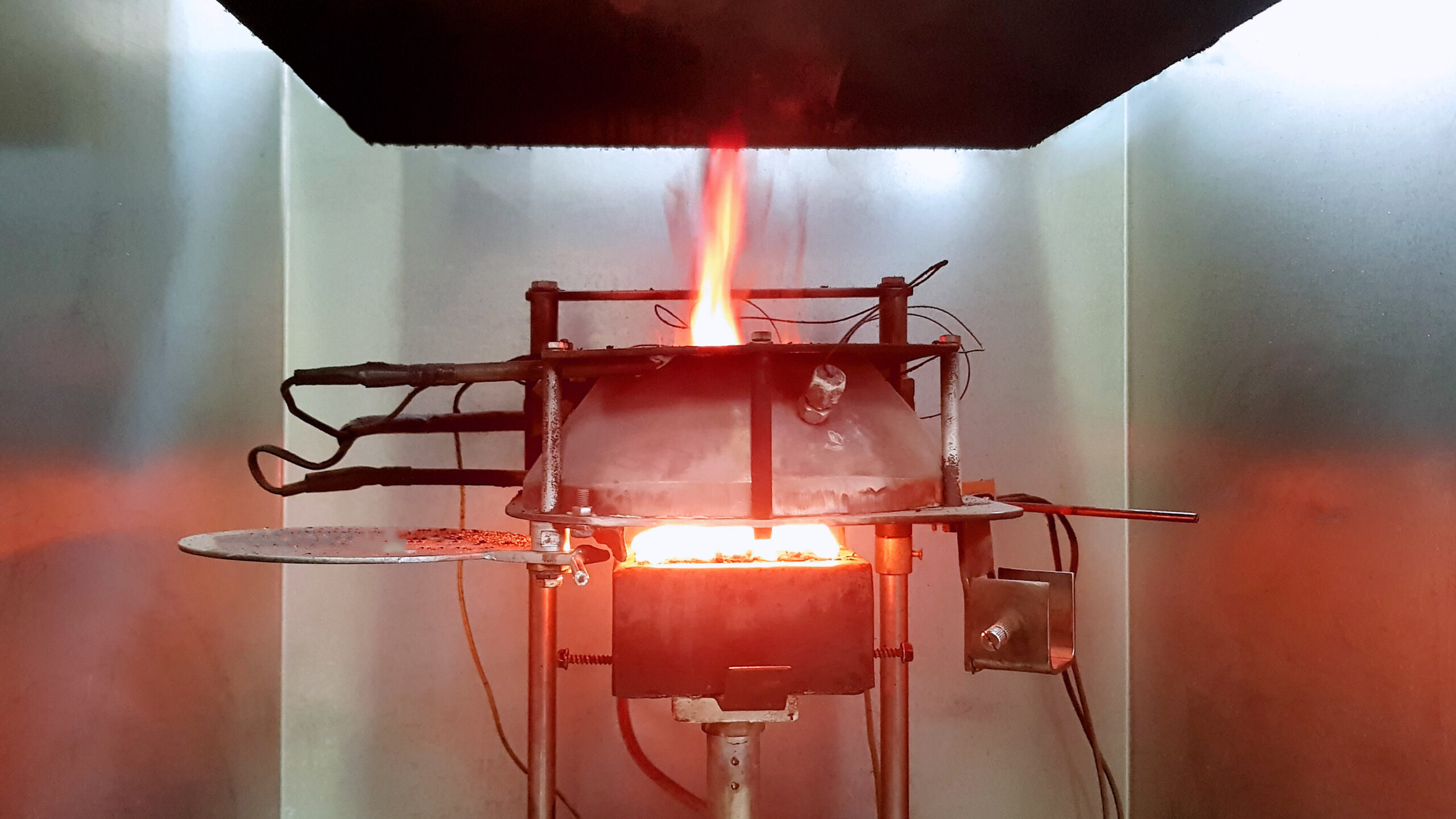
Stale rozwijając technologię i funkcjonalność naszych produktów, mamy okazję spełniać kolejne normy. Dzięki temu stajemy się transportem przyszłości – i to w najbezpieczniejszy możliwy sposób.
Aktualności
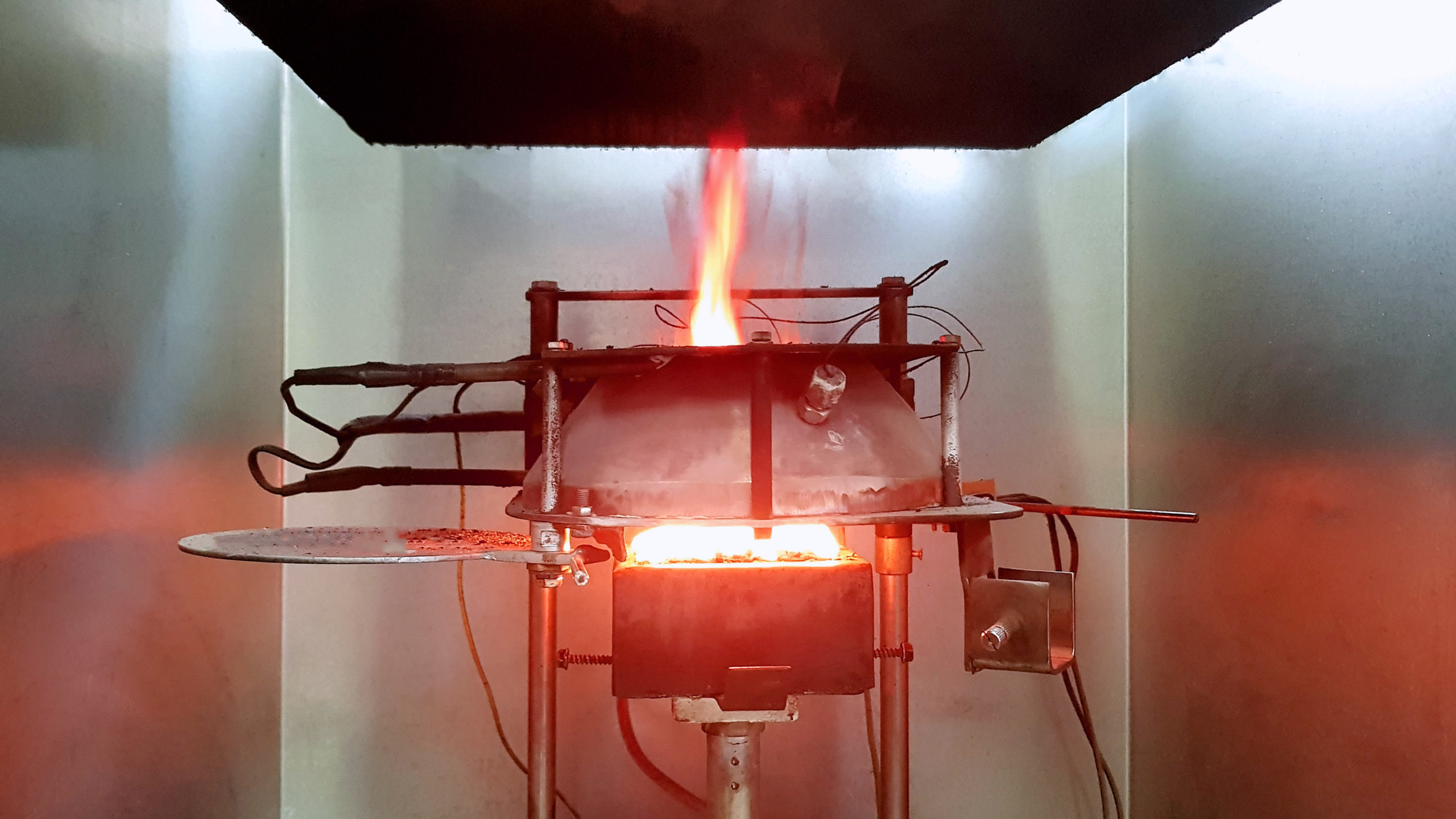
Pomimo obecnej sytuacji na świecie aktywność działu R&D naszej firmy nie zwalnia, a nawet i nabiera rozpędu. Przez ostatnie tygodnie inżynierowie oddziału w Mielcu zajmowali się badaniem, testowaniem i opracowywaniem nowoczesnych rozwiązań. Wszystko po to, by metodycznie poszerzać ofertę o kolejne produkty – funkcjonalne i bezpieczne.
Praca nad nowymi koncepcjami to wieloetapowy proces, który wymaga zaangażowania specjalistów z różnych dziedzin, doskonałej organizacji czasu i umiejętności patrzenia na materiały z różnych perspektyw. Od zawsze stanowiła trzon naszego rozwoju, dlatego ostatni kwartał poświęciliśmy temu, by dostarczać klientom rozwiązania nie tylko spełniające ich potrzeby, ale i wyprzedzające je.
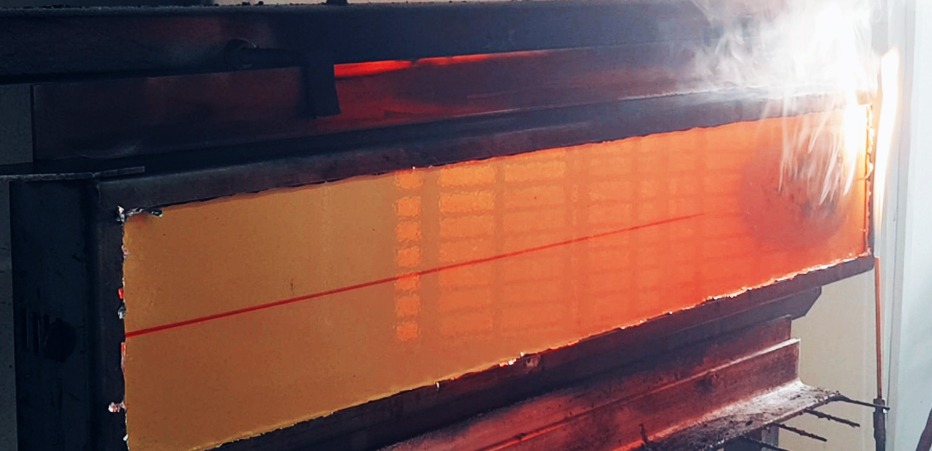
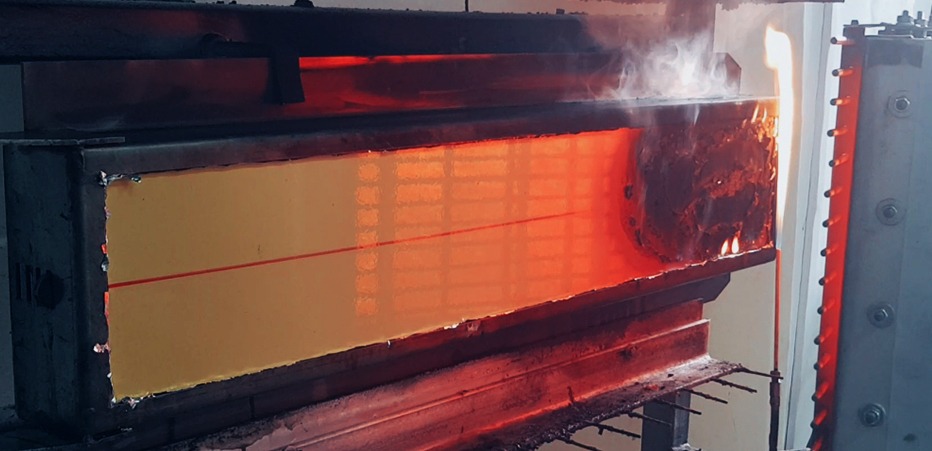
Podczas prac zespołu technologów i inżynierów dostrzeżono ogromny potencjał ’w obszarach związanych z ognioodpornością, wytrzymałością materiałów na rozciąganie i odpornością na warunki atmosferyczne:
- systemów żywicznych – poszukiwaliśmy najlepszych kombinacji wzmocnień, przeprowadzając testy mechaniczne i kondensacji,
- folii nawierzchniowych – które mogą optymalizować proces produkcji prze zastąpienie/uzupełnienie procesu lakierowania,
- sfer szklanych i innych komponentów – zwiększających sztywność i zmniejszających palność.
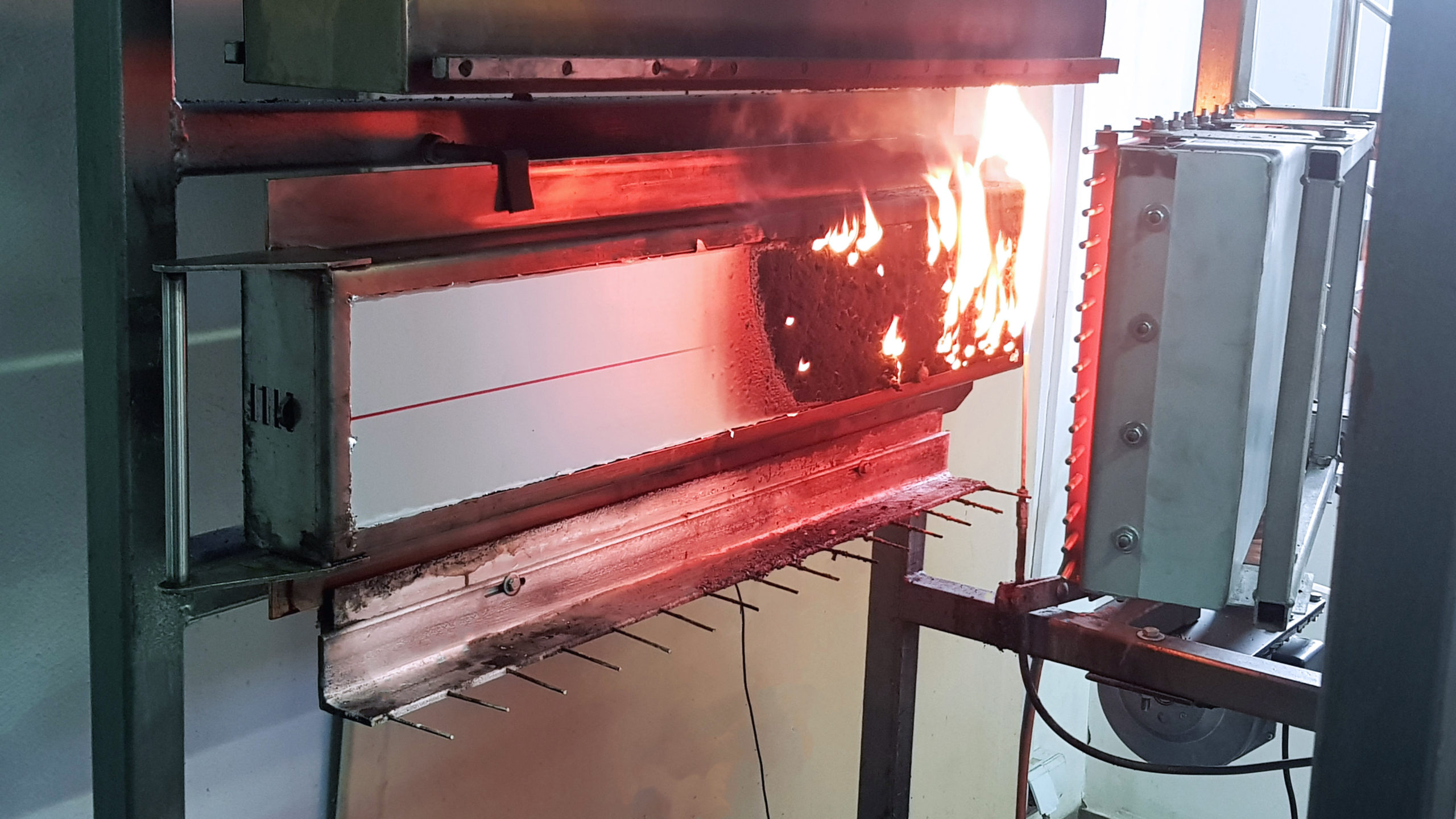
Wynikiem wzmożonej pracy są sukcesy na polu uzyskania poziomu HL3 R1 normy palnościowej EN-45545-2 dla wnętrza naszych pojazdów. Kolejnym krokiem będzie uzyskanie odpowiednich parametrów kompozytów, które pozwolą na produkcję elementów warstwowych typu ‘’sandwich’’ mających zastosowanie w kabinach, dachach, podłogach, ścianach bocznych i komponentach podwozia systemu XBODY.