Author: Mariola Moskal
News
News
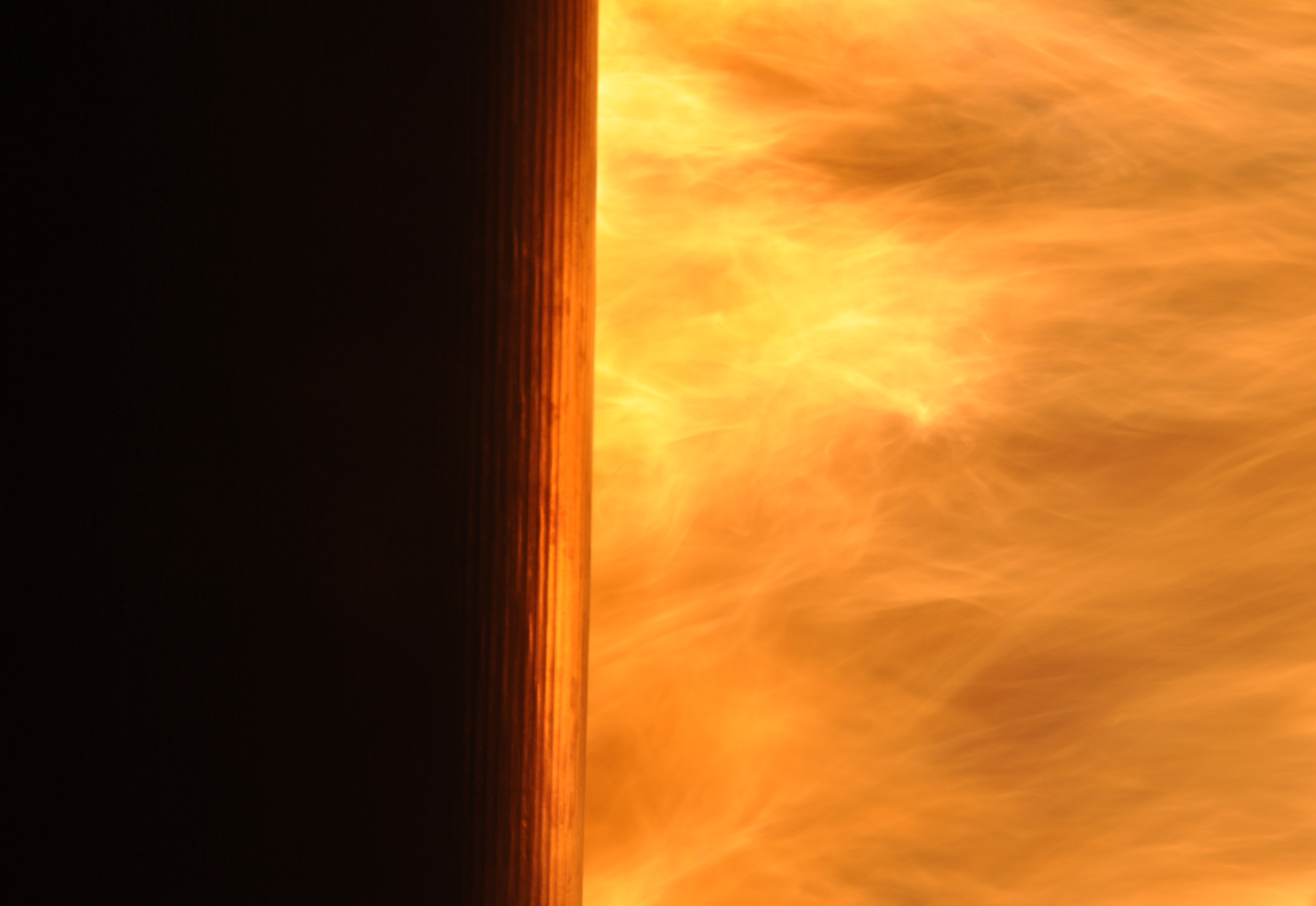
Another month and another goal reached by 3A Composites Mobility team. With proud and pleasure we inform about the achievement of HL3 level regarding EN-45545 based on non-phenolic components. It is the highest level for R17 in EN 45545 standard – the complete system including painting. Because we ensure high quality of our products, our system do not contain phenolic based materials. Thanks to this success, we are able to produce sandwich elements which will be applicable to the front ends of rail vehicles including subway metro systems.
Fire protection for railway vehicles – EN45545 standard– clarifies the material requirements for different levels of risk regarding various parts of vehicles. Recent weeks our engineers have been working in order to achieve another goal according to our projects and, in consequence, to continually develop innovative solutions for the future of transport.
There were a number of tests intensively conducted in accordance with regulation in authorized laboratories in order to obtain the highest quality of components delivered to our clients.
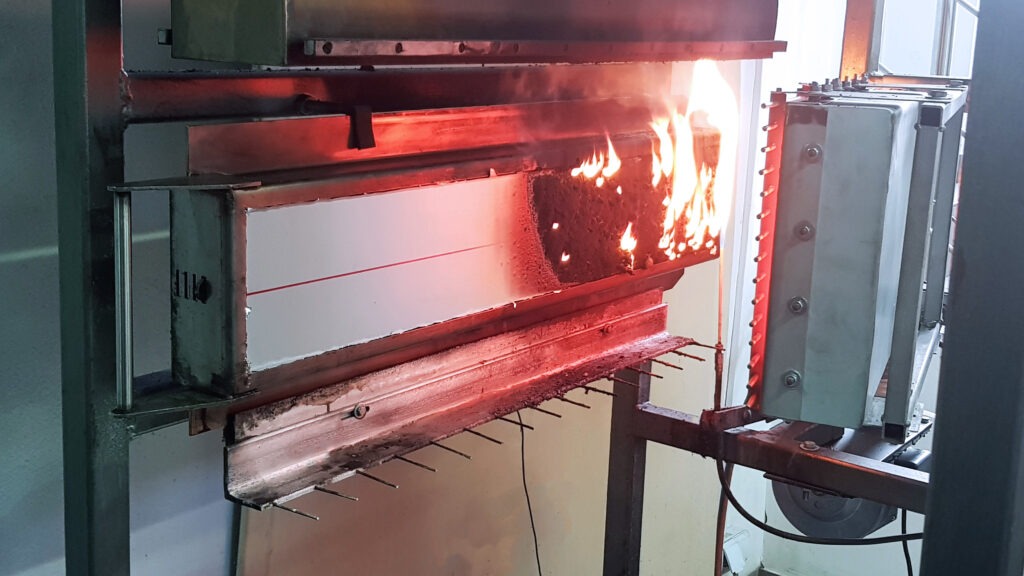
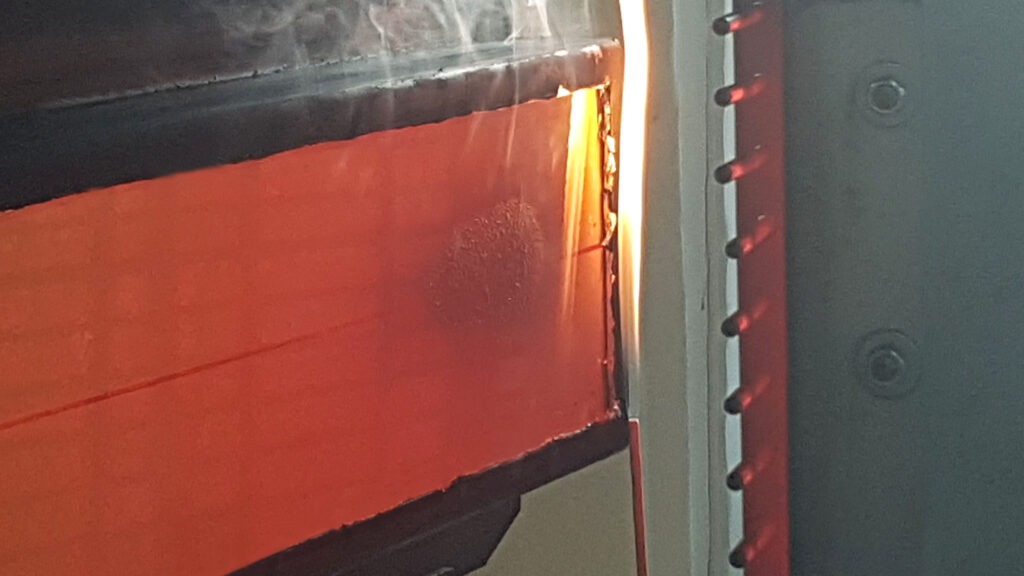
The following researches were carried out:
1. CFE-ISO 5658-2 – The flame spread
The principle is the propagation of flame alongside the sample until it becomes extinct or test is completed. The method enables to define the length of the burned part of the sample to specify a critical heat flux (kW/m2). The approach is conducted in order to term the spread of flame.
2. MAHRE ISO 5660-1 – The heat release intensity
Regarding this test, the sample is treated with ionizing radiation by using an electric conical heater. This process controls the maximum average rate of heat release (kW/m2) throughout 20-minute test. The analysis is intended to determine the intensity of heat release by the sample.
3. Ds./VOF/CIT ISO 5659-2 – The intensity of smoke production
The sample is treated with thermal radiation in a closed chamber with the aim of testifying gross optical density Ds and VOF4 – blackout value at fourth minute. The test specifies concentration of relevant fumes in emitted smoke and defines the toxicity index of the gases – CITG (-). The method allows to calculate the rate of smoke production.
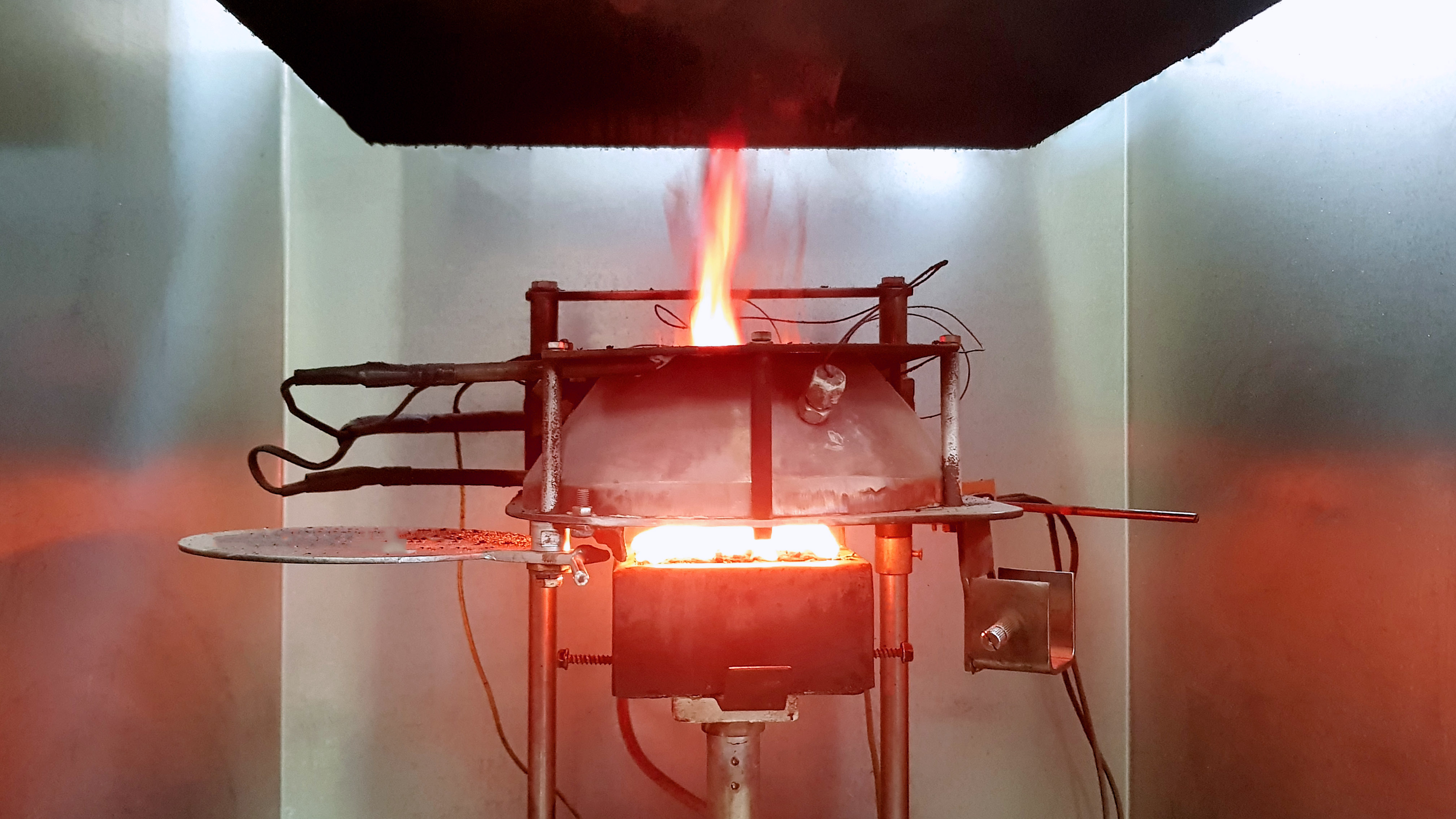
Due to continuous development of technology and functionality of our products, we have opportunity to comply with next railway standards. Owing to this, we contribute the future of transport – and in the safest possible way.
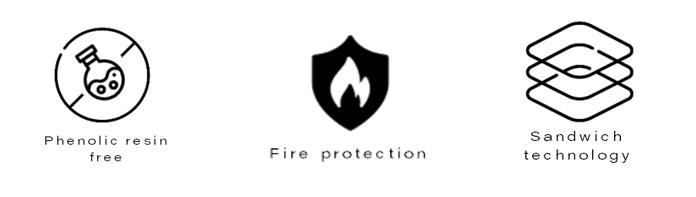
News
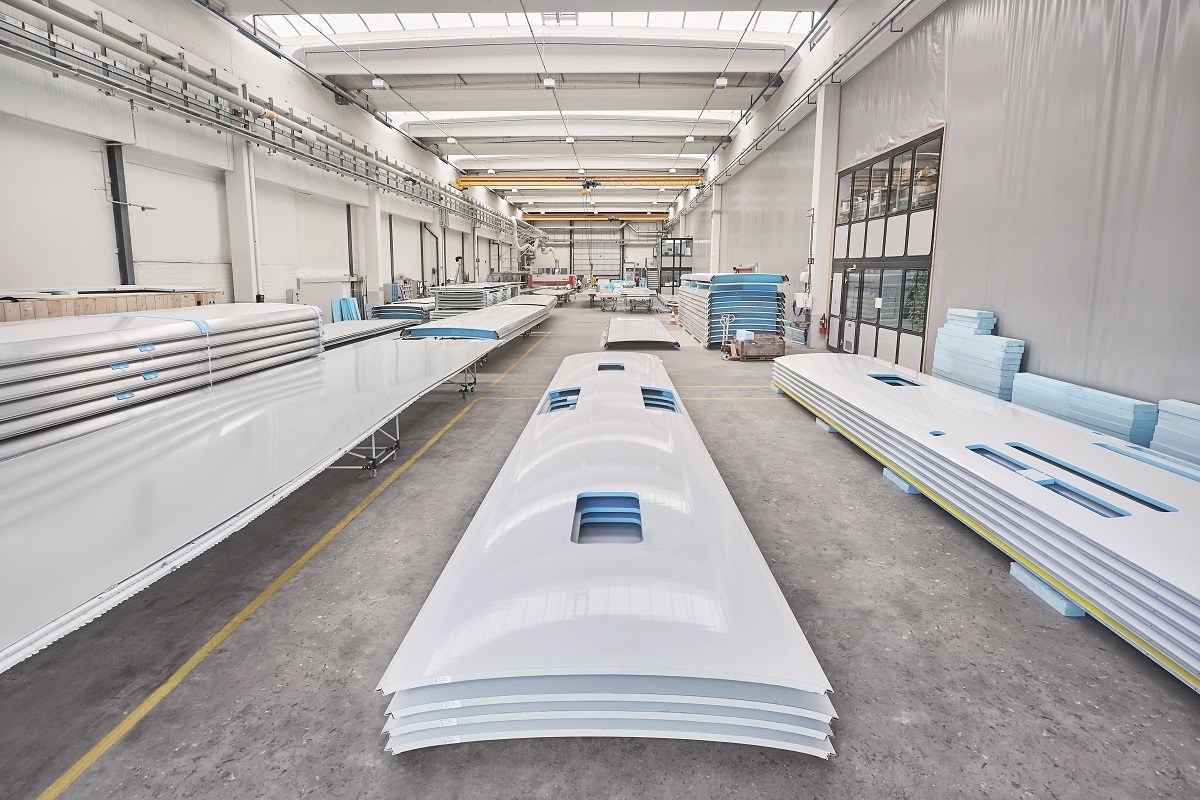
The tightening of the fire protection regulation in buses according to ECE R118-3, 2018 leads to a further increased passenger safety.
3A Composites Mobility has extensive experience in the material selection for metal/foam based sandwich systems as well as for painted reinforced plastic composite systems. With our XBODY applications we meet the increased requirements for flammability, low heating fire release value, fire spread, smoke and toxicity. The type approval was carried out by TÜV SÜD and includes applications for roofs, sidewalls, interdecks, floors as well as for engine compartments and battery cases.
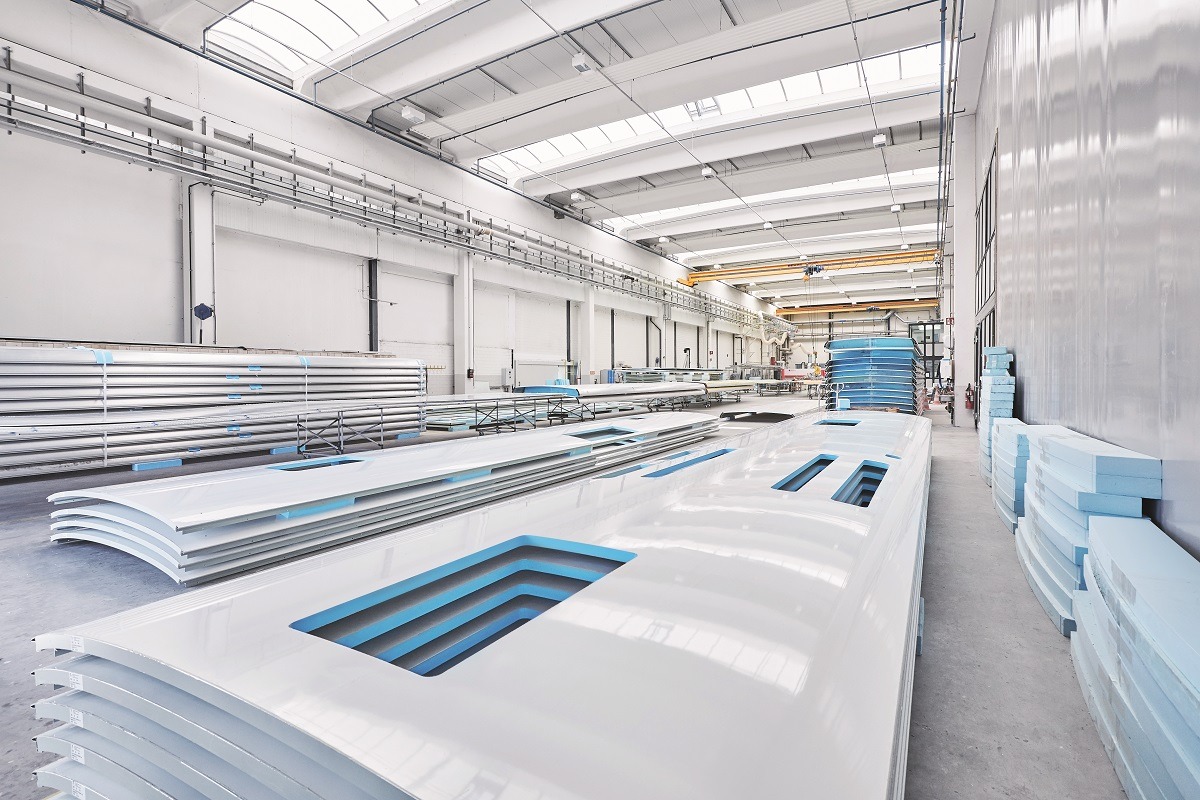
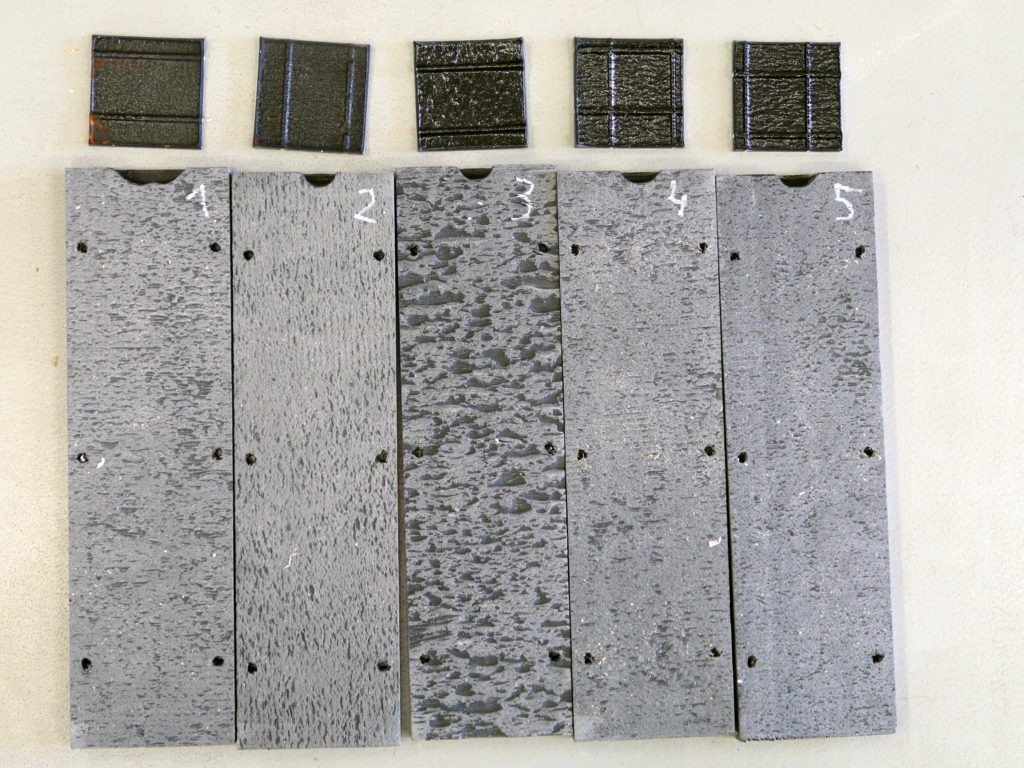
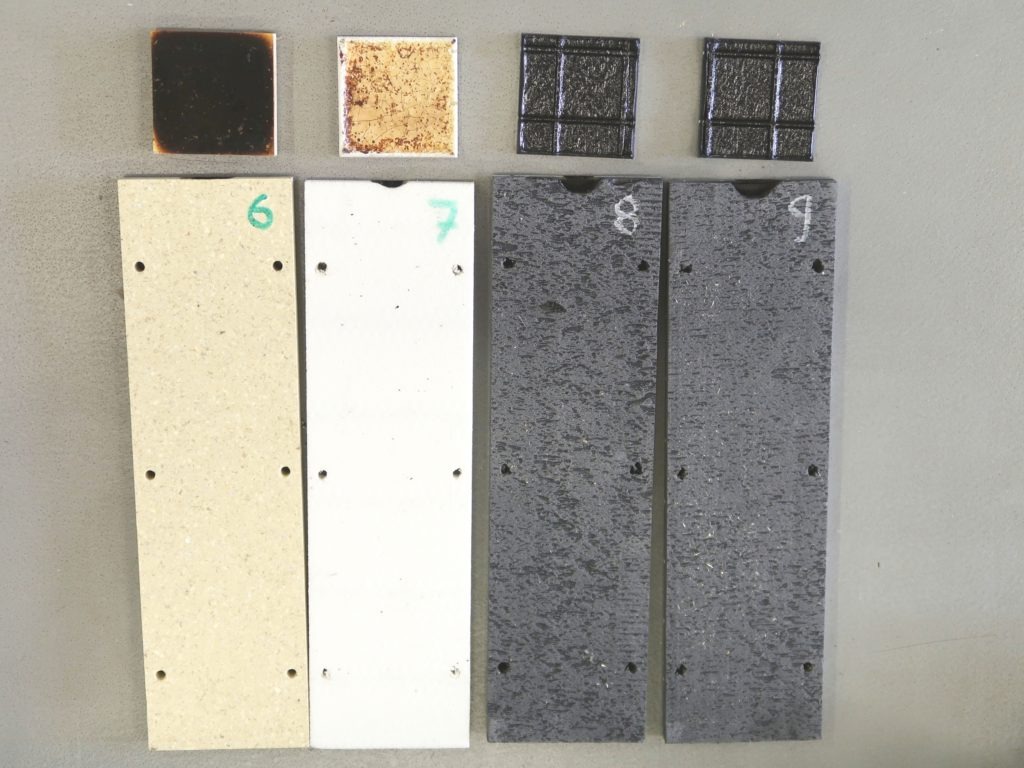
News
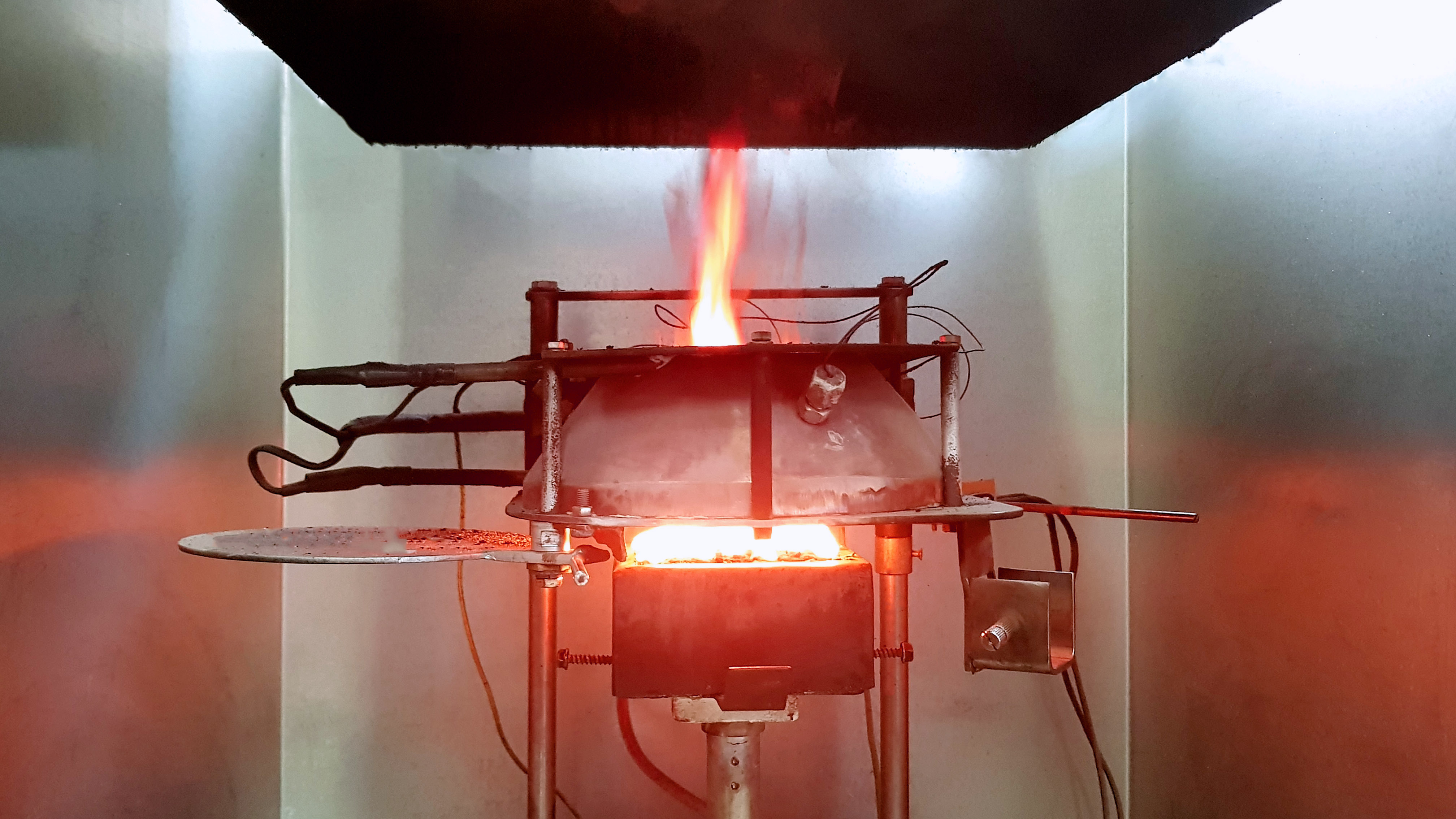
Despite the current world situation, the activity of our R&D department is not slowing down. Indeed, R&D is gaining momentum. The engineers from 3A Composites Mobility division in Mielec have been developing, testing and devising modern solutions for last weeks. All that to methodologically expand our offer with further products – functional and safe.
Working on novel concepts is the multiple stage process which requires the involvement of specialists in various fields, perfect time organization and the ability of analyzing materials from different perspectives. Because R&D has always been the core of development, we devoted the last quarter to provide customers with solutions which not only meet the customers’ needs, but also exceed customer expectations.
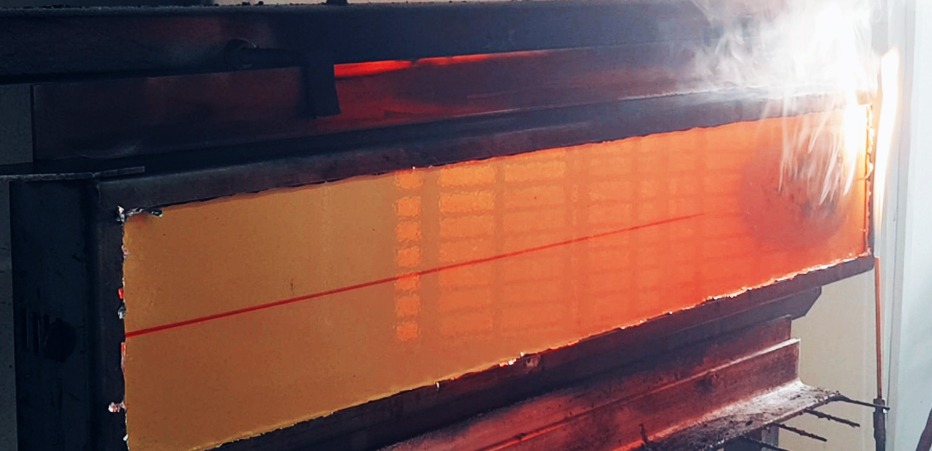
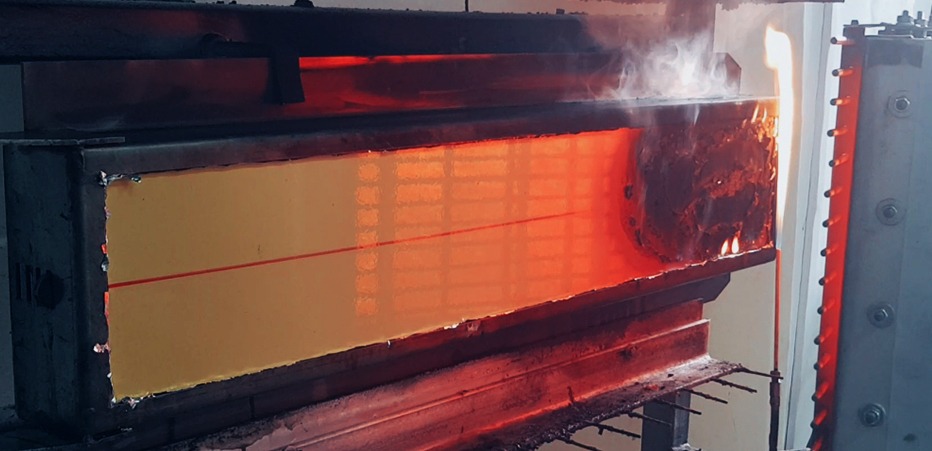
During the work of the team of engineers and technologists, there was the greatest potential recognized in the areas of fire resistance, the tensile strength of material and resistance to atmospheric conditions:
- resin systems – conducting mechanical and condensation tests, we searched for the best combinations of reinforcements
- surface foils – which would optimize the production process by replacing/complementing the lacquering process
- glass spheres and other components – which increase the stiffness and which are flame retardants
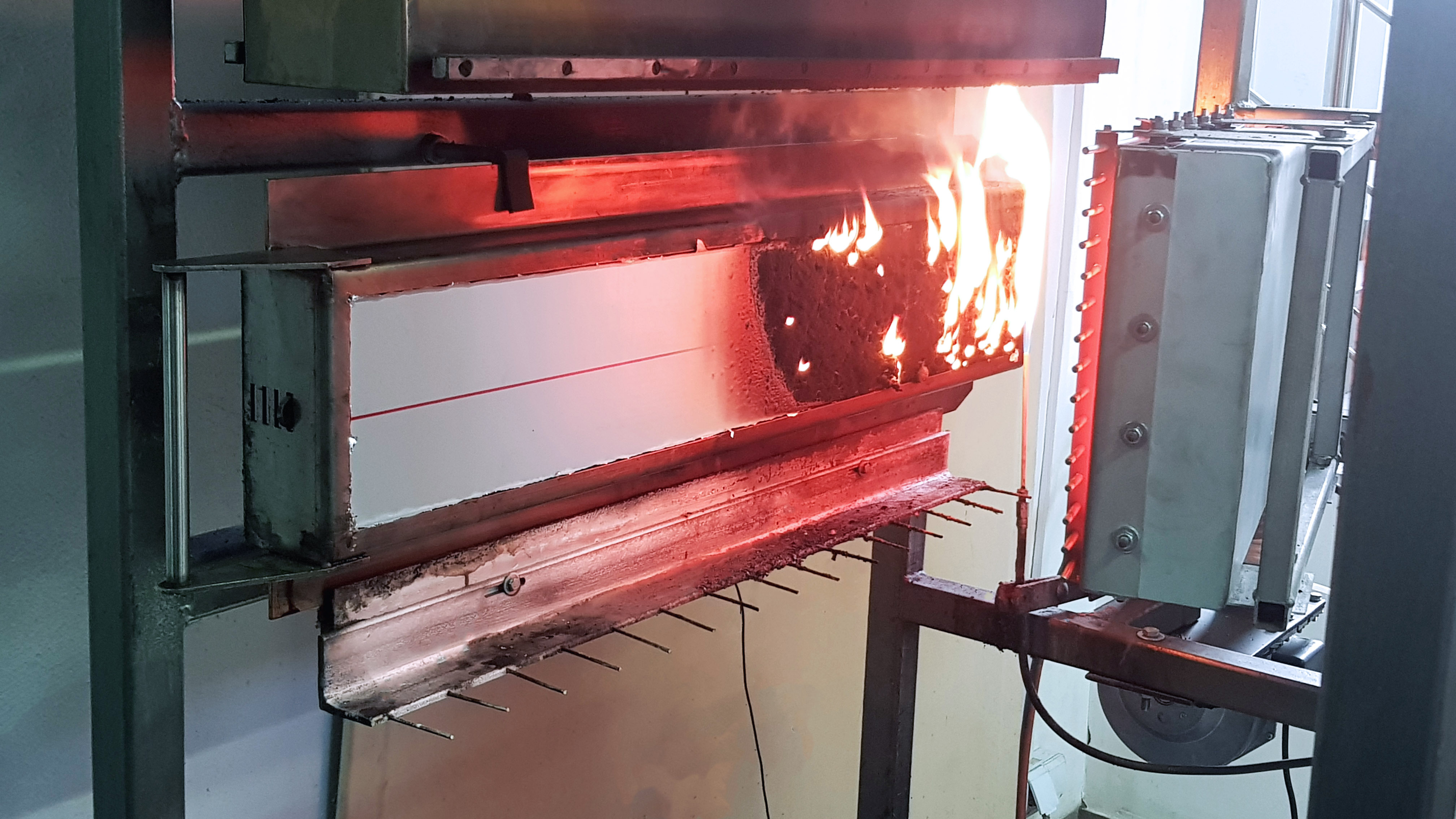
The results of enhanced efforts are successes in the area of reaching the HL3 R1 level regarding EN45545-2 flammability standard for interior fittings of railway vehicles. The next step will be to acquire the relevant parameters of composites which allow the production of the sandwich elements which are applicable in cabins, roofs, floors, sidewalls and undercarriage components regarding XBODY system.
News
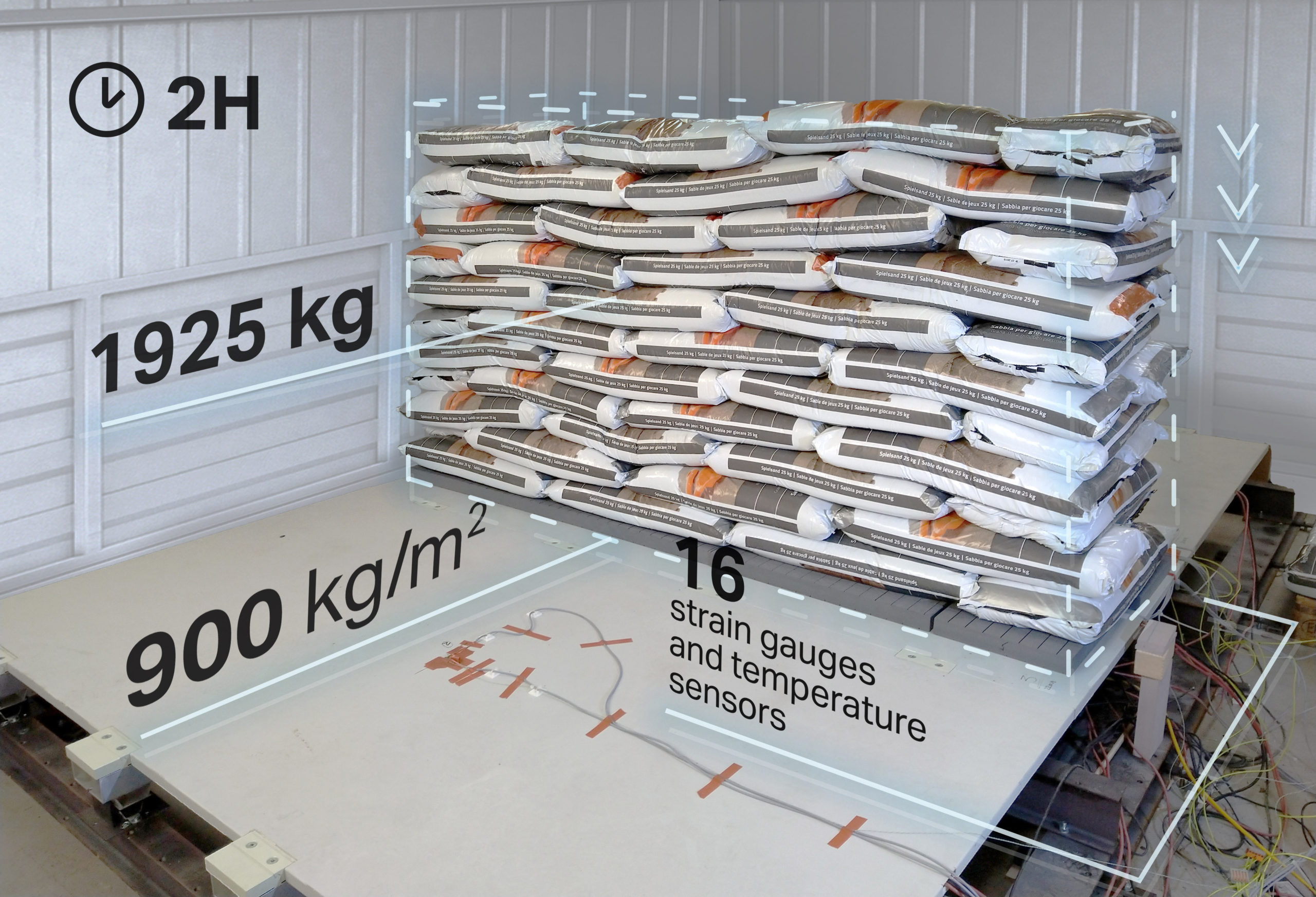
Can you improve something that is flawlessly designed and works great in use? It turns out that it is possible – by all means. The COMFLOOR has been in service for more than ten years enjoying the trust of many railways manufacturers for a wide range of rail vehicles including trams and double-deckers trains. The absence of any failures allows us to improve the product for usability.
The goal of the optimization is to enhance the already strong capabilities of the current product. We’ve always been a customer-centric company that wants to deliver the most technologically advanced product with reasonable price. Considering all the highest quality and value, of course. Cost reduction in design and assembly at the customer was one of our initial goals. And it went perfectly well.

What are the most important changes and what do you gain from the latest improvements to the COMFLOOR heated floor systems?
The new mounting system allows shorter assembly times and improves the stiffness as well as strength of the panels. This enables larger span widths and even reduction of the support structure which leads to a lighter and more economical vehicle as less material is required. As they say, less is more! Furthermore, the slimmer design increases the space for passengers. In addition, the results of high acoustic performance have been significantly improved. That’s not everything. The improvements are not limited to technical performance.
The supply network and manufacturing processes are carefully rebalanced to allow a high degree of customization and at the same time standardize as many components as possible for cost-effectiveness. Prototypes of the new design were successfully tested. The panels withstood a load of two tons without any indication of fractures. This translates to a passenger load of 900 kg per square meter. You can’t disagree that it’s a lot.
Introduced changes and new advanced improvements open up many new possibilities for your production. Contact us to learn more about the COMFLOOR.